A Solid Is Crushed To A Powder
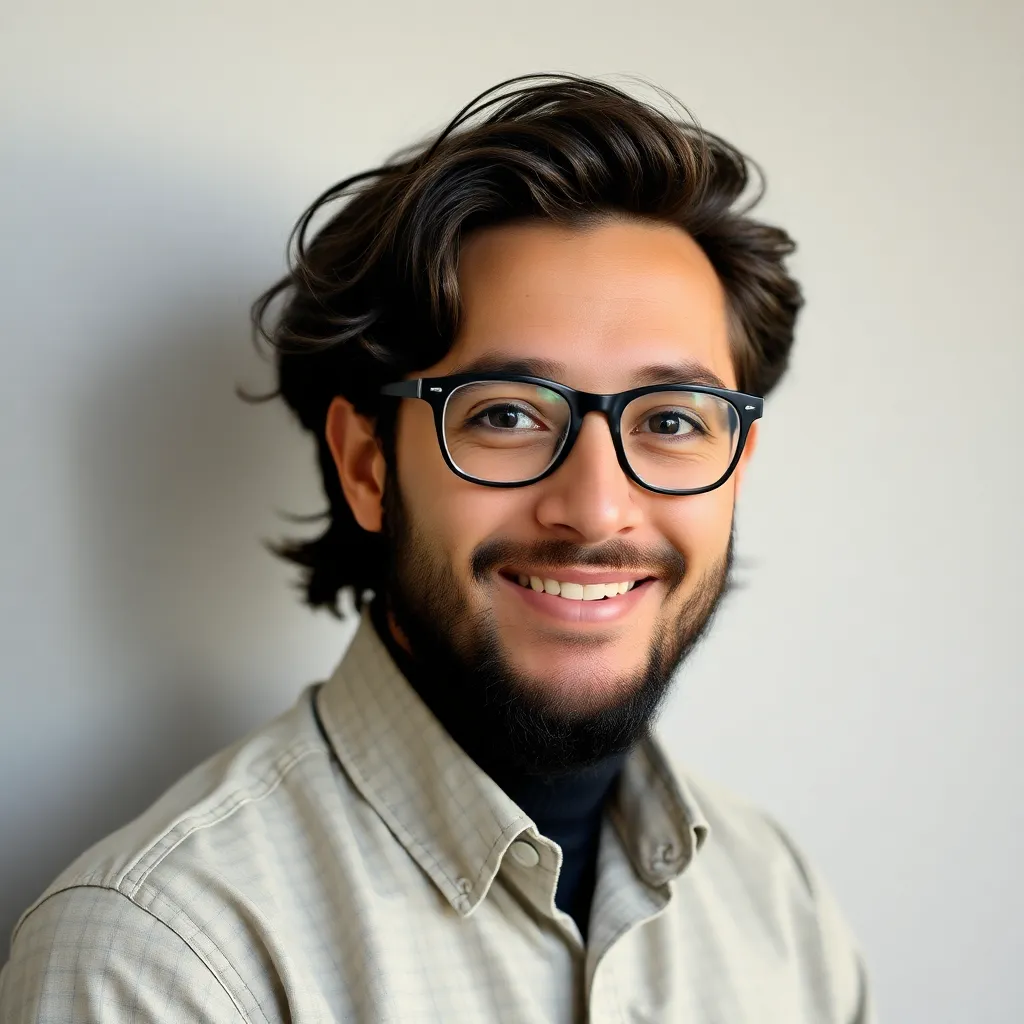
Kalali
Apr 10, 2025 · 5 min read
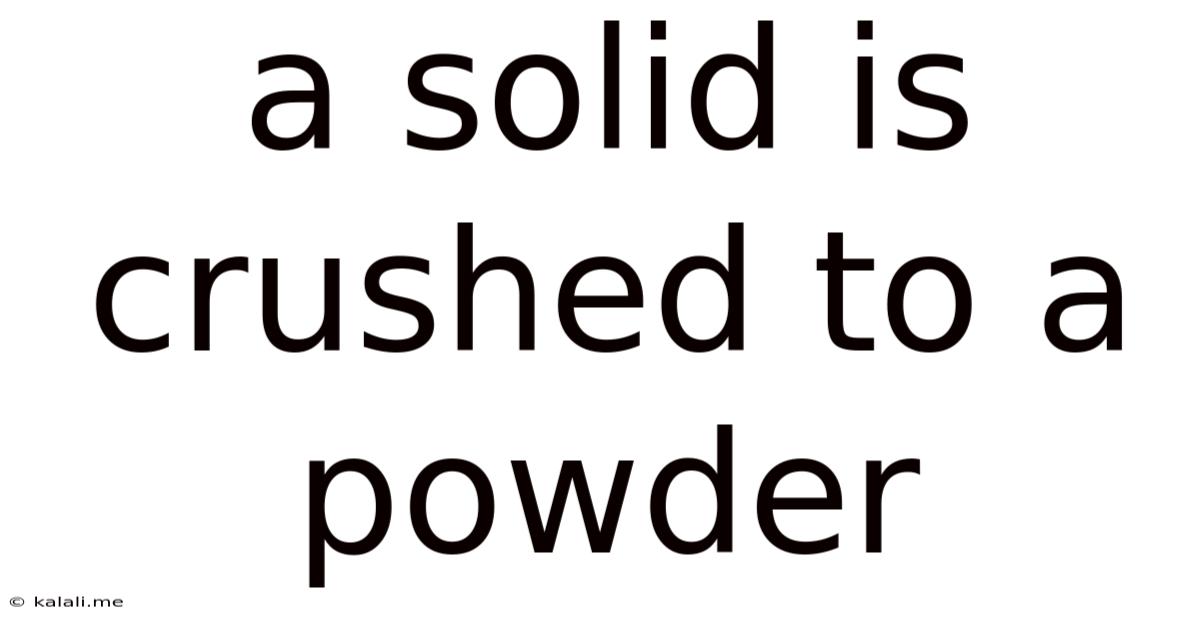
Table of Contents
When a Solid is Crushed to a Powder: A Deep Dive into Comminution
The seemingly simple act of crushing a solid into a powder belies a complex interplay of physics, chemistry, and engineering. This seemingly mundane process, often termed comminution, is fundamental to numerous industries, from mining and pharmaceuticals to food processing and construction. Understanding the mechanisms involved, the influencing factors, and the resulting properties is crucial for optimizing efficiency and achieving desired product characteristics. This article delves into the multifaceted world of comminution, exploring the science behind it and its widespread applications.
What is Comminution?
Comminution, from the Latin "comminuere" meaning "to break into small pieces," encompasses all processes that reduce the size of solid materials. This reduction can range from coarse crushing of large rocks to the fine grinding of minerals or pharmaceuticals to a powdery consistency. The process fundamentally alters the surface area of the material, significantly impacting its reactivity, solubility, and other physical properties.
Mechanisms of Size Reduction:
The size reduction of a solid involves overcoming the inherent forces holding its constituent particles together. These forces can be broadly classified as:
-
Fracture: The breaking of a solid into smaller pieces due to applied stress exceeding its tensile strength. This is the primary mechanism in many comminution processes. Fracture can occur through various modes, including tensile, shear, and compressive fracture, depending on the nature of the applied force and the material's properties. Brittle materials tend to fracture readily, while ductile materials deform plastically before fracturing.
-
Attrition: The wearing away of material through friction and impact. This mechanism is particularly important in fine grinding processes where particles repeatedly collide with each other or with grinding surfaces. Attrition contributes significantly to the generation of fine powders.
-
Abrasion: Similar to attrition, abrasion involves the removal of material by rubbing or scraping against a harder surface. This mechanism is prevalent in processes involving grinding media, such as ball mills, where the particles are ground against each other and against the mill lining.
-
Impact: The sudden application of a large force to a solid, causing it to fracture or shatter. Impact is a crucial mechanism in processes like hammer mills and impact crushers.
Factors Influencing Comminution:
Numerous factors influence the effectiveness and efficiency of comminution processes. These include:
-
Material Properties: The inherent properties of the solid material significantly dictate its susceptibility to size reduction. These properties include:
- Hardness: Harder materials require more energy to crush than softer materials.
- Brittleness: Brittle materials fracture easily, while ductile materials deform plastically.
- Toughness: Tough materials resist fracture and require significant energy for size reduction.
- Particle size distribution: The initial size distribution of the material affects the energy required for further size reduction.
- Moisture content: Moisture can influence the strength and fracture behavior of materials.
-
Process Parameters: The parameters of the comminution process itself heavily influence its outcome:
- Type of equipment: Different types of comminution equipment (e.g., jaw crushers, cone crushers, ball mills, roller mills) employ different mechanisms and are suited to different materials and size reduction targets.
- Particle size reduction ratio: The ratio between the initial and final particle size influences the energy requirements.
- Energy input: The amount of energy applied per unit mass of material directly affects the degree of size reduction.
- Time: The duration of the comminution process influences the extent of size reduction.
Types of Comminution Equipment:
A wide range of equipment is employed for comminution, each designed for specific applications and material characteristics:
-
Crushers: Used for primary size reduction of large materials. Examples include jaw crushers, cone crushers, gyratory crushers, and impact crushers.
-
Grinders: Used for finer size reduction, often producing powders. Examples include ball mills, rod mills, vibratory mills, hammer mills, and roller mills.
-
Other equipment: Other specialized equipment includes ultrafine grinders, jet mills, and attritors, used for producing extremely fine particles.
Applications of Comminution:
Comminution is a cornerstone process across diverse industries:
-
Mining: Crushing and grinding ores to liberate valuable minerals.
-
Cement production: Grinding raw materials like limestone and clay to create cement clinker.
-
Pharmaceuticals: Reducing the size of active pharmaceutical ingredients (APIs) to improve their dissolution and bioavailability.
-
Food processing: Grinding grains, spices, and other food materials to create powders or pastes.
-
Construction: Crushing aggregates for concrete and asphalt production.
-
Ceramic industry: Grinding raw materials for ceramic production.
-
Chemical industry: Comminution is crucial in the production of various chemicals and materials.
Energy Considerations:
Comminution is an energy-intensive process. A significant portion of the energy input is consumed in overcoming the material's inherent strength and generating new surfaces. Optimizing comminution processes involves minimizing energy consumption while achieving the desired size reduction. This often requires careful selection of equipment and process parameters, alongside a thorough understanding of the material's properties.
Scale-up and Modeling:
Scaling up comminution processes from laboratory to industrial scales requires careful consideration of the factors influencing size reduction. Mathematical models are often used to predict the performance of comminution equipment at different scales. These models take into account factors such as material properties, process parameters, and equipment design.
Particle Size Analysis:
Determining the particle size distribution of the resulting powder is crucial for quality control and process optimization. Various techniques are used for particle size analysis, including sieving, laser diffraction, and image analysis. The resulting data provides insights into the effectiveness of the comminution process and the properties of the final product.
Environmental Considerations:
Comminution processes can generate dust, noise, and vibrations, presenting environmental concerns. Dust suppression techniques, noise reduction measures, and vibration isolation are essential for minimizing the environmental impact of comminution operations. The disposal of waste materials generated during comminution also requires careful management.
Emerging Technologies:
Recent advancements in comminution technology focus on enhancing efficiency, reducing energy consumption, and improving environmental performance. These include the development of new comminution equipment, advanced control systems, and the application of innovative techniques like high-pressure homogenization and cryogenic grinding. Research into the application of ultrasound and microwaves for enhancing comminution efficiency is also ongoing.
Conclusion:
Crushing a solid into a powder is far more than a simple act; it's a complex engineering and scientific process with significant industrial implications. Understanding the mechanisms of comminution, the factors influencing size reduction, and the characteristics of different comminution equipment is crucial for optimizing efficiency, minimizing energy consumption, and ensuring product quality across a vast array of industries. As technology continues to evolve, the field of comminution promises further innovation, leading to more efficient, sustainable, and precise size reduction techniques. The seemingly simple act of transforming a solid into a powder holds the key to numerous advancements in diverse technological fields.
Latest Posts
Latest Posts
-
39 Degrees Celsius Converted To Fahrenheit
Apr 18, 2025
-
Identify The Type Of Function Represented By
Apr 18, 2025
-
3 1 4 As Improper Fraction
Apr 18, 2025
-
136 Minutes In Hours And Minutes
Apr 18, 2025
-
What Is The Greatest Common Factor Of 6 And 15
Apr 18, 2025
Related Post
Thank you for visiting our website which covers about A Solid Is Crushed To A Powder . We hope the information provided has been useful to you. Feel free to contact us if you have any questions or need further assistance. See you next time and don't miss to bookmark.