A Warehouse Received 250 Orders In April
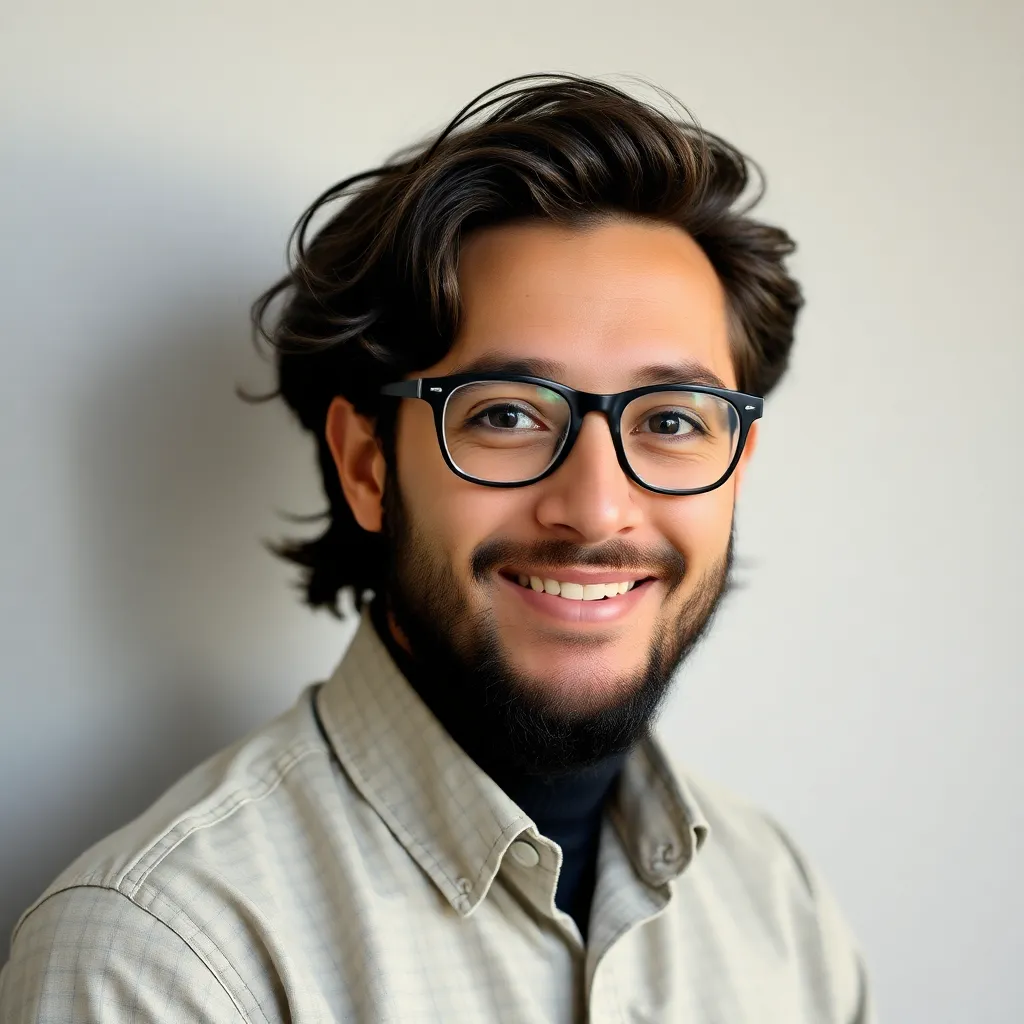
Kalali
Jul 10, 2025 · 6 min read
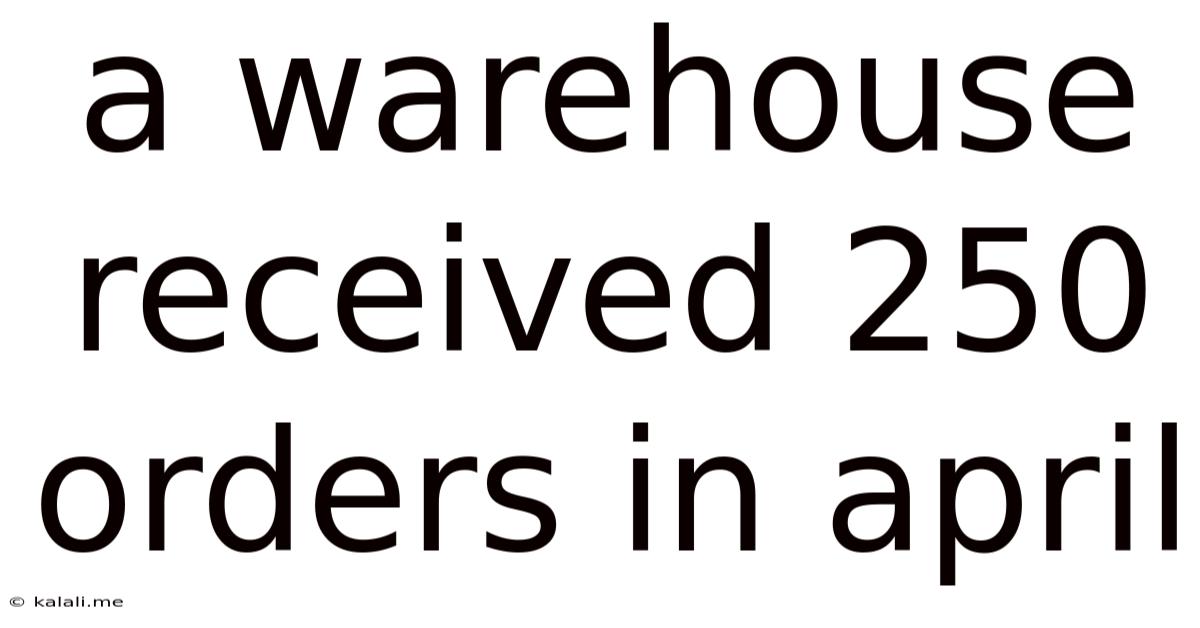
Table of Contents
A Warehouse Received 250 Orders in April: Unpacking the Data and Optimizing for Growth
Meta Description: Analyzing a warehouse's April performance of 250 orders reveals key insights for optimizing logistics, inventory management, and overall operational efficiency. This detailed analysis explores potential bottlenecks, strategies for improvement, and future growth projections.
Receiving 250 orders in April might seem like a relatively modest number for a warehouse, but the true significance lies not in the raw figure itself, but in the context it provides. This single data point unlocks a wealth of opportunities for analysis, leading to improvements in efficiency, profitability, and long-term growth. To truly understand the implications of receiving 250 orders in April, we need to delve deeper into the various aspects of warehouse operation and performance.
Understanding the Context: Beyond the Numbers
Before jumping into solutions, we need a clearer picture. The 250 orders represent a snapshot of activity. To make this data meaningful, we need additional information:
- Year-over-year comparison: How does April's performance compare to April of the previous year? An increase might signal growth, while a decrease could indicate underlying problems.
- Order volume trends: What's the overall trend in order volume over the past few months or years? Is this a peak, a trough, or part of a consistent pattern?
- Order size and type: Were these 250 orders all small, individual purchases, or did they include large, bulk orders? This dramatically impacts warehouse operations.
- Product mix: Which products were most frequently ordered? Analyzing this helps identify popular items and potential inventory management issues.
- Average order fulfillment time: How long did it take to process and ship each order? Slow fulfillment times can impact customer satisfaction and repeat business.
- Inventory levels: Were there any stockouts or excessive inventory of specific items? Effective inventory management directly relates to order fulfillment.
- Warehouse size and layout: The physical limitations of the warehouse can significantly affect processing capacity.
- Staffing levels: Were there enough employees to handle the order volume? Understaffing can lead to delays and errors.
- Technology used: The use of Warehouse Management Systems (WMS), automated picking systems, or other technologies drastically impacts efficiency.
- Shipping methods: Which carriers were used, and what were the associated costs? Understanding shipping expenses is crucial for profitability.
By gathering this supplementary data, we can move beyond the surface-level number of 250 orders and gain a comprehensive understanding of the warehouse's performance.
Analyzing Bottlenecks and Potential Problems
Let's assume, for the sake of this analysis, that the 250 orders represent a slight decrease compared to last April and that the average order fulfillment time was higher than the target. This points to potential bottlenecks within the warehouse operation. Several areas warrant closer examination:
- Inefficient Picking and Packing Processes: Manual processes are often slower and more prone to errors than automated systems. Analyzing the picking routes, packing procedures, and the overall workflow can reveal opportunities for optimization. Could implementing pick-to-light systems or voice-directed picking improve efficiency?
- Inventory Management Issues: Stockouts lead to lost sales and dissatisfied customers. Excessive inventory ties up capital and increases storage costs. Analyzing inventory turnover rates, using ABC analysis to prioritize high-value items, and implementing just-in-time inventory management strategies could be beneficial.
- Lack of Proper Storage Solutions: Inefficient storage solutions waste space and time. Optimizing shelf placement, implementing vertical storage, and using efficient racking systems can significantly improve warehouse productivity.
- Technology Gaps: The lack of a robust WMS or other technological solutions can hinder efficiency. Investing in appropriate technology can automate many processes, reducing manual errors and improving overall speed.
- Insufficient Staffing: If the staff is overloaded, it can lead to delays and increased error rates. Analyzing labor productivity and considering additional staffing or cross-training could be necessary.
- Poor Warehouse Layout: A poorly designed warehouse layout can lead to unnecessary movement and wasted time. Re-evaluating the layout to optimize workflow and minimize travel distances is crucial.
- Shipping and Logistics Challenges: High shipping costs or unreliable carriers can impact profitability and customer satisfaction. Exploring alternative shipping options and negotiating better rates with carriers can be beneficial.
Strategies for Improvement and Optimization
Based on the potential bottlenecks identified, several strategies can be implemented to improve warehouse efficiency and performance:
1. Implementing a Warehouse Management System (WMS): A WMS streamlines operations by automating various tasks, including inventory management, order tracking, and shipping. This can significantly reduce manual errors and improve efficiency. Features such as real-time inventory tracking, automated picking lists, and integrated shipping labels will dramatically speed up the process.
2. Optimizing Inventory Management: Implementing ABC analysis to categorize inventory based on value and usage allows for focused attention on high-value items. Just-in-time inventory management minimizes storage costs and reduces the risk of obsolescence. Regular stock audits can help identify discrepancies and improve accuracy.
3. Improving Picking and Packing Processes: Implementing techniques such as batch picking, zone picking, and wave picking can significantly improve picking efficiency. Investing in automated picking systems or voice-directed picking technology can further enhance speed and accuracy. Optimizing packing materials and procedures can minimize waste and improve packaging speed.
4. Enhancing Warehouse Layout and Design: A well-designed warehouse layout minimizes travel time and maximizes space utilization. Strategies such as implementing cross-docking, optimizing aisle widths, and utilizing vertical space can improve efficiency. Consider implementing lean warehouse methodologies to eliminate waste and improve workflow.
5. Leveraging Technology: Exploring options beyond a WMS, such as RFID tracking, automated guided vehicles (AGVs), and robotic process automation (RPA) can further automate tasks and improve efficiency. Data analytics tools can help identify trends and patterns, allowing for proactive adjustments to operations.
6. Optimizing Staffing and Training: Adequate staffing levels are critical for handling peak order volumes. Cross-training employees to handle multiple tasks can increase flexibility and improve overall productivity. Investing in employee training can improve skills and efficiency.
7. Streamlining Shipping and Logistics: Negotiating better rates with carriers, exploring alternative shipping methods, and optimizing packaging can reduce shipping costs. Implementing a robust shipping management system can improve tracking and reduce delays.
Forecasting Future Growth and Capacity Planning
Analyzing the 250 orders in April, along with the historical data and the implemented improvements, allows for more accurate forecasting of future order volume. This is crucial for capacity planning. Several techniques can be used for forecasting:
- Time series analysis: Analyzing historical order data to identify trends and seasonal patterns.
- Regression analysis: Identifying relationships between order volume and other factors, such as marketing campaigns or economic indicators.
- Moving averages: Smoothing out fluctuations in order volume to identify underlying trends.
- Exponential smoothing: Giving more weight to recent data in the forecast.
Accurate forecasting enables proactive capacity planning. This includes:
- Staffing adjustments: Adjusting staffing levels to meet projected order volume.
- Warehouse expansion: Planning for potential warehouse expansion to accommodate future growth.
- Technology investments: Investing in new technologies to handle increased order volume.
- Inventory management strategies: Adjusting inventory levels to meet anticipated demand.
Conclusion: Turning Data into Actionable Insights
The seemingly simple statistic of 250 orders in April provides a rich foundation for improving warehouse operations. By analyzing the data within its context and identifying potential bottlenecks, we can develop targeted strategies for optimization. Implementing these strategies, coupled with accurate forecasting, enables proactive capacity planning and sustainable growth. Remember, the key is to move beyond the raw numbers and focus on the actionable insights they reveal. Continuously monitoring key performance indicators (KPIs) and adapting strategies as needed is vital for long-term success. Turning data into actionable insights is the key to unlocking the full potential of your warehouse.
Latest Posts
Latest Posts
-
700 Is 10 Times As Much As
Jul 12, 2025
-
How Much Is 120 Kilograms In Pounds
Jul 12, 2025
-
Born In 1990 How Old Am I
Jul 12, 2025
-
What Is The Average Iq For A 5 Year Old
Jul 12, 2025
-
How Many 12 Oz Cups In A Gallon
Jul 12, 2025
Related Post
Thank you for visiting our website which covers about A Warehouse Received 250 Orders In April . We hope the information provided has been useful to you. Feel free to contact us if you have any questions or need further assistance. See you next time and don't miss to bookmark.