Porous Water Absorbing Mass Of Fibers Formula
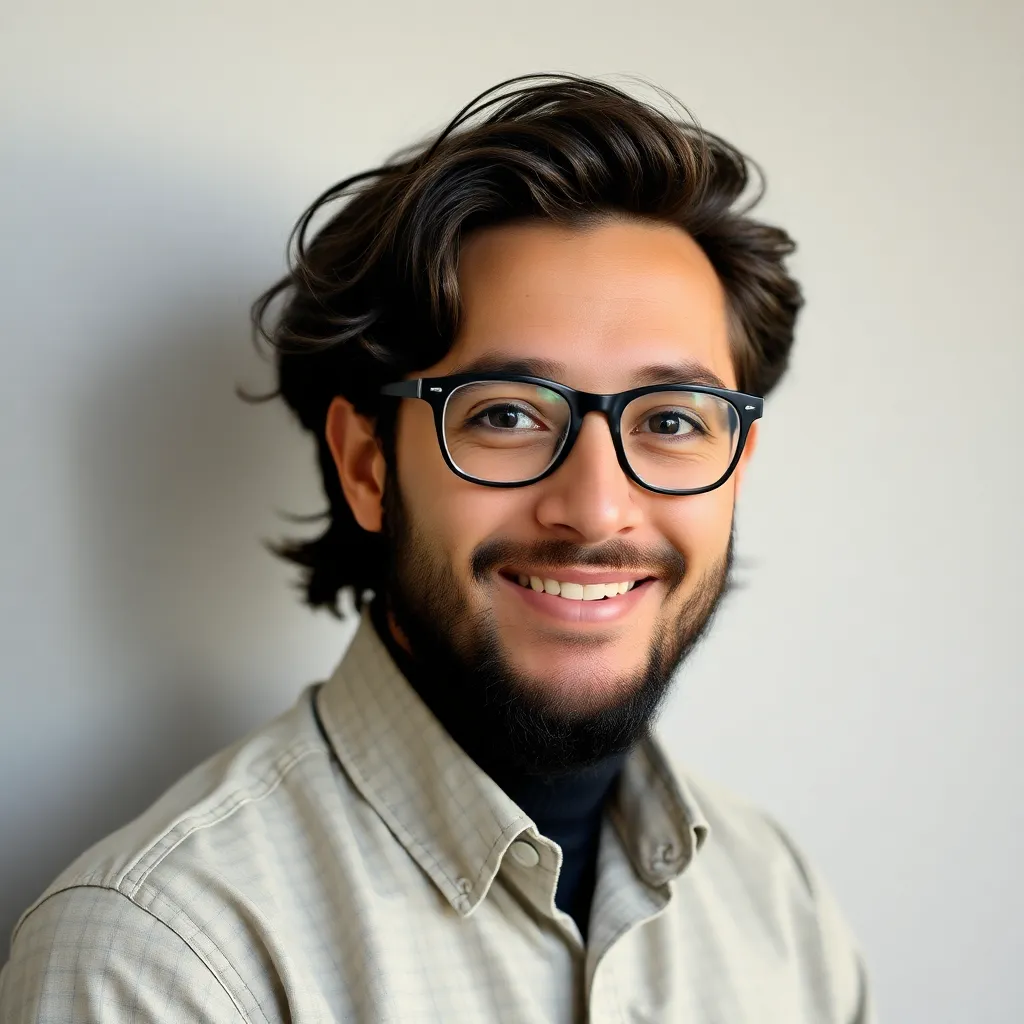
Kalali
Jun 30, 2025 · 7 min read

Table of Contents
Decoding the Formula: Porous Water-Absorbing Masses of Fibers
The seemingly simple concept of a porous, water-absorbing mass of fibers belies a complex interplay of material science, engineering, and chemistry. This article delves into the multifaceted formula behind these materials, exploring the types of fibers used, the manufacturing processes involved, and the key properties that determine their effectiveness in various applications. From everyday uses like diapers and sanitary products to advanced applications in agriculture and environmental remediation, understanding the formula behind these absorbent materials is crucial. This exploration will cover everything from the fundamental fiber characteristics to the sophisticated designs that optimize water absorption and retention.
What Makes a Fiber Water-Absorbent?
The ability of a fiber to absorb water hinges on several key characteristics:
-
Fiber Type: The inherent properties of the fiber itself play a critical role. Cellulose fibers, like those derived from cotton, wood pulp, and bamboo, are naturally hydrophilic (water-loving) due to their abundance of hydroxyl (-OH) groups. These groups form hydrogen bonds with water molecules, facilitating absorption. Synthetic fibers, such as polyesters and polyamides, are generally hydrophobic (water-repelling) unless modified chemically. However, through processes like grafting or blending with hydrophilic polymers, their absorbency can be significantly enhanced.
-
Fiber Morphology: The physical structure of the fiber impacts its absorbency. Fibers with high surface area, such as those with a porous or crimped structure, offer more sites for water molecules to interact. Surface roughness and the presence of microfibrils further enhance capillary action, drawing water into the fiber's interior. The fiber diameter also plays a role; finer fibers often exhibit higher surface area-to-volume ratios and thus better absorbency.
-
Fiber Treatment: Chemical treatments can significantly alter a fiber's absorbency. For example, treating cellulose fibers with specific chemicals can increase their hydrophilicity and improve their ability to swell upon water absorption. Similarly, grafting hydrophilic polymers onto synthetic fibers can transform them from water-repellent to water-absorbent.
The Formula: A Blend of Science and Engineering
The "formula" for a porous, water-absorbing mass of fibers is not a single equation, but rather a complex interplay of factors including:
-
Fiber Selection: The choice of fibers is dictated by the desired application. For hygiene products, high-absorbency cellulose fibers are commonly employed, often blended with superabsorbent polymers (SAPs) to enhance their capacity. Agricultural applications might utilize fibers derived from agricultural waste, creating a sustainable and cost-effective solution.
-
Fiber Arrangement: How the fibers are arranged in the mass greatly influences the final product's properties. Randomly arranged fibers create a porous structure with high absorbency but potentially lower structural integrity. More structured arrangements, achieved through techniques like needle punching or hydroentanglement, can provide both high absorbency and enhanced strength.
-
Binding Agents: Binding agents are often incorporated to hold the fibers together, creating a cohesive mass. These agents can be natural or synthetic polymers, chosen based on their compatibility with the fibers and the desired properties of the final product. The choice of binding agent influences the absorbency, strength, and overall performance of the absorbent mass.
-
Superabsorbent Polymers (SAPs): These are high-molecular-weight polymers with an exceptional ability to absorb and retain large quantities of liquid. SAPs are frequently incorporated into absorbent masses to boost their absorption capacity. They work by absorbing water into their three-dimensional network of cross-linked polymers. Different types of SAPs offer varying levels of absorption and retention, allowing for customization depending on the application.
-
Additives: Additional components are sometimes added to modify the properties of the absorbent mass. These could include:
- Antibacterial agents: to inhibit the growth of bacteria.
- Softening agents: to enhance the comfort and softness of the material.
- Fragrances: to improve the odor of the product.
- Colorants: to provide the desired color.
Manufacturing Processes: Transforming Fibers into Absorbent Masses
The transformation of individual fibers into a functional absorbent mass involves various manufacturing processes:
-
Carding and Blending: Fibers are initially carded to align and disentangle them, creating a uniform web. Blending different fiber types is often necessary to optimize the final product's properties. This step is crucial for creating consistent fiber distribution within the absorbent mass.
-
Web Formation: The blended fibers are then formed into a web, which can be done using different techniques, including air-laying, wet-laying, or spunlace processes. Air-laying uses air streams to create a randomly arranged fiber web, while wet-laying involves dispersing fibers in a liquid medium and then draining off the liquid. Spunlace employs high-pressure water jets to entangle the fibers, creating a non-woven fabric.
-
SAP Incorporation: SAP granules are typically incorporated into the fiber web during or after web formation. Uniform distribution of SAPs is crucial for optimal absorption. Advanced techniques are often employed to ensure the SAPs are evenly dispersed and do not clump together.
-
Calendering: This process involves passing the fiber web between rollers under pressure to consolidate the structure and improve its strength and uniformity. The level of calendering affects the final product's softness and absorbency.
-
Converting: The consolidated web is then converted into the desired shape and size, such as sheets, pads, or other forms. This step frequently involves cutting, folding, and packaging processes tailored to the specific application.
Applications Across Diverse Industries
The applications of porous, water-absorbing masses of fibers are vast and varied:
-
Hygiene Products: Diapers, sanitary napkins, and incontinence products rely heavily on these materials for their absorbency and comfort. The high absorption capacity and retention of these materials ensures the products are effective and comfortable for the user. The focus here is on high absorption, quick wicking, and superior softness.
-
Agriculture: These materials can be used in hydroponics and soil amendment to improve water retention and nutrient delivery to plants. Their ability to retain moisture allows for reduced water consumption and improved crop yields. The materials are selected for their compatibility with plants and soil environment.
-
Environmental Remediation: Absorbent materials can be used to clean up spills of oil, chemicals, and other pollutants. Their high absorbency helps contain and remove these substances, preventing environmental contamination. The key here is the absorbency of specific substances, and the resistance to degradation in challenging environmental conditions.
-
Medical Applications: These materials are used in wound dressings to absorb exudates and promote healing. Their ability to absorb liquids while maintaining breathability aids in wound care. Sterility and biocompatibility are crucial aspects of medical applications.
-
Industrial Applications: They are used in various industrial settings for cleaning, absorbing spills, and other applications requiring high absorbency. Their ability to wick away liquids is useful in various manufacturing processes. Resistance to chemicals and degradation are crucial in industrial applications.
Future Trends and Innovations:
Research and development continue to push the boundaries of water-absorbing materials:
-
Bio-based Fibers: The focus is on developing sustainable and environmentally friendly absorbent materials using fibers derived from renewable resources. This reduces reliance on petroleum-based materials and minimizes environmental impact.
-
Advanced Polymer Chemistry: New polymer chemistries are constantly being explored to create SAPs with even higher absorption capacities and improved properties like temperature resistance and biodegradability.
-
Nanotechnology: Nanomaterials are being investigated to enhance the absorbency and other properties of absorbent materials, leading to smaller, more efficient, and effective products.
-
Smart Materials: The integration of sensors and other smart technologies is exploring the possibilities of creating absorbent materials that can monitor and regulate their performance based on real-time needs.
In conclusion, the formula for a porous, water-absorbing mass of fibers is not a simple equation but a complex interplay of fiber selection, arrangement, processing, and additive incorporation. Understanding this interplay is vital for developing high-performance absorbent materials tailored to specific applications. As research continues, we can expect further advancements in materials science and engineering to create even more effective and sustainable absorbent masses that meet the diverse needs of our world.
Latest Posts
Latest Posts
-
How Many Bottles Of Water Are In A Liter
Jul 01, 2025
-
How Many Days Are In 16 Years
Jul 01, 2025
-
List The Following Events In The Correct Chronological Order
Jul 01, 2025
-
How To Know When Chorizo Is Done
Jul 01, 2025
-
Volume Is The Amount Of What In An Object
Jul 01, 2025
Related Post
Thank you for visiting our website which covers about Porous Water Absorbing Mass Of Fibers Formula . We hope the information provided has been useful to you. Feel free to contact us if you have any questions or need further assistance. See you next time and don't miss to bookmark.