Stress Strain Diagram For Ductile Material
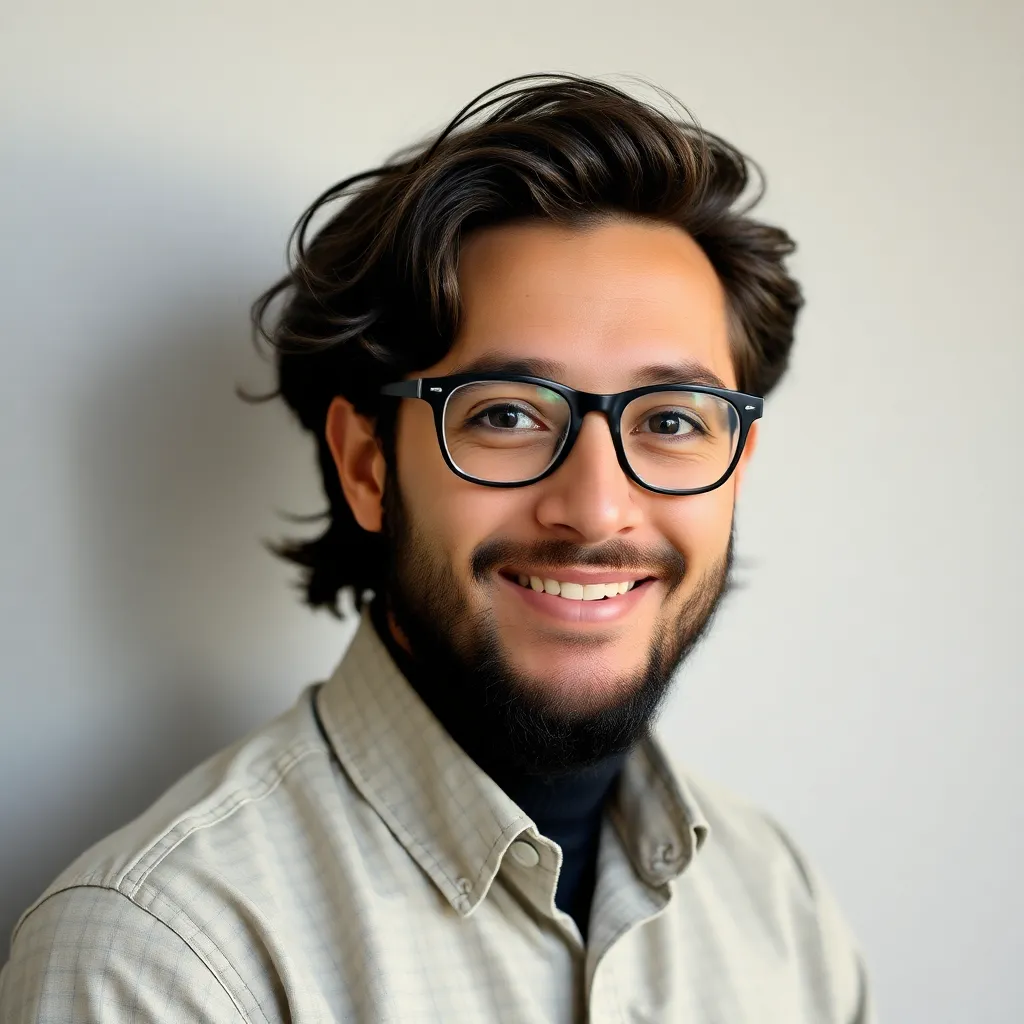
Kalali
Jun 11, 2025 · 4 min read

Table of Contents
Understanding the Stress-Strain Diagram for Ductile Materials
The stress-strain diagram is a fundamental concept in materials science, providing crucial insights into a material's mechanical behavior under load. This article will delve into the specifics of the stress-strain diagram for ductile materials, explaining its key features and what they signify for engineering applications. Understanding this diagram is essential for selecting appropriate materials for various engineering designs, ensuring structural integrity and preventing failure.
What is a Stress-Strain Diagram?
A stress-strain diagram graphically represents the relationship between stress (force per unit area) and strain (deformation per unit length) of a material when subjected to a tensile test. The test involves gradually applying a tensile load to a specimen and measuring the resulting elongation. This data is then plotted to create the diagram. The shape and characteristics of this diagram reveal much about the material's properties, particularly its strength, ductility, and toughness.
Key Regions of the Ductile Material Stress-Strain Diagram
The stress-strain curve for a ductile material typically exhibits several distinct regions:
-
Elastic Region: In this initial region, the material behaves elastically, meaning it deforms proportionally to the applied stress and returns to its original shape once the load is removed. This linear relationship is governed by Young's modulus (E), also known as the modulus of elasticity, which represents the material's stiffness. The point where the elastic region ends is the proportional limit.
-
Yield Point: Beyond the proportional limit, the material begins to deform plastically. This means permanent deformation occurs, and the material won't return to its original shape even after the load is removed. The yield strength (σy) is the stress at which this plastic deformation begins. This is often defined as the 0.2% offset yield strength, a practical measure used because the transition from elastic to plastic deformation isn't always sharply defined.
-
Strain Hardening (Work Hardening): After the yield point, further stress increases cause continued plastic deformation. However, the material resists further deformation, requiring progressively higher stress to achieve additional strain. This phenomenon is called strain hardening or work hardening. The slope in this region indicates the material's resistance to further plastic deformation.
-
Ultimate Tensile Strength: This point represents the maximum stress the material can withstand before necking begins. Ultimate tensile strength (UTS) is a crucial design parameter, indicating the maximum load a material can carry before failure.
-
Necking: After the ultimate tensile strength is reached, the material begins to neck, meaning a localized reduction in cross-sectional area occurs. This localized deformation leads to a decrease in the load-bearing capacity, even though the stress might seem to decrease on the stress-strain curve.
-
Fracture: Finally, the material fractures, marking the end of the tensile test. The total elongation up to fracture is a measure of the material's ductility.
Significance of the Stress-Strain Diagram for Ductile Materials
The stress-strain diagram is invaluable for:
-
Material Selection: Engineers use it to compare the properties of different materials and choose the most suitable one for a specific application based on required strength, ductility, and toughness.
-
Design Considerations: The diagram helps engineers determine the maximum allowable stress and strain for a component under different loading conditions, preventing failure during service.
-
Quality Control: The stress-strain curve can be used to assess the quality and consistency of materials during manufacturing.
-
Failure Analysis: Examining the fracture point and the overall curve can provide valuable insights into the causes of material failure.
Understanding Ductility and its importance
Ductility, as mentioned earlier, is a key characteristic reflected in the stress-strain diagram. High ductility materials exhibit significant plastic deformation before fracture, making them suitable for applications requiring formability, such as drawing wires or forming sheets. Conversely, brittle materials show little to no plastic deformation before fracture.
In conclusion, the stress-strain diagram is a powerful tool providing critical insights into the mechanical behavior of ductile materials. Understanding its features and interpreting the data it provides is paramount for engineers and materials scientists in designing safe and reliable structures and components. The concepts of Young's Modulus, Yield Strength, Ultimate Tensile Strength, and ductility are all critical parameters derived directly from this diagram, enabling informed decision-making throughout the design process.
Latest Posts
Latest Posts
-
How Many Quarts Is In 64 Ounces
Jul 01, 2025
-
What Is 1 And 1 4 Cup In Half
Jul 01, 2025
-
How Many Chicken Drumettes In A Pound
Jul 01, 2025
-
How Much Is A Quarter Million Dollars
Jul 01, 2025
-
How Many Laps Around A Basketball Court Is A Mile
Jul 01, 2025
Related Post
Thank you for visiting our website which covers about Stress Strain Diagram For Ductile Material . We hope the information provided has been useful to you. Feel free to contact us if you have any questions or need further assistance. See you next time and don't miss to bookmark.