Stress Strain Graph For Ductile Material
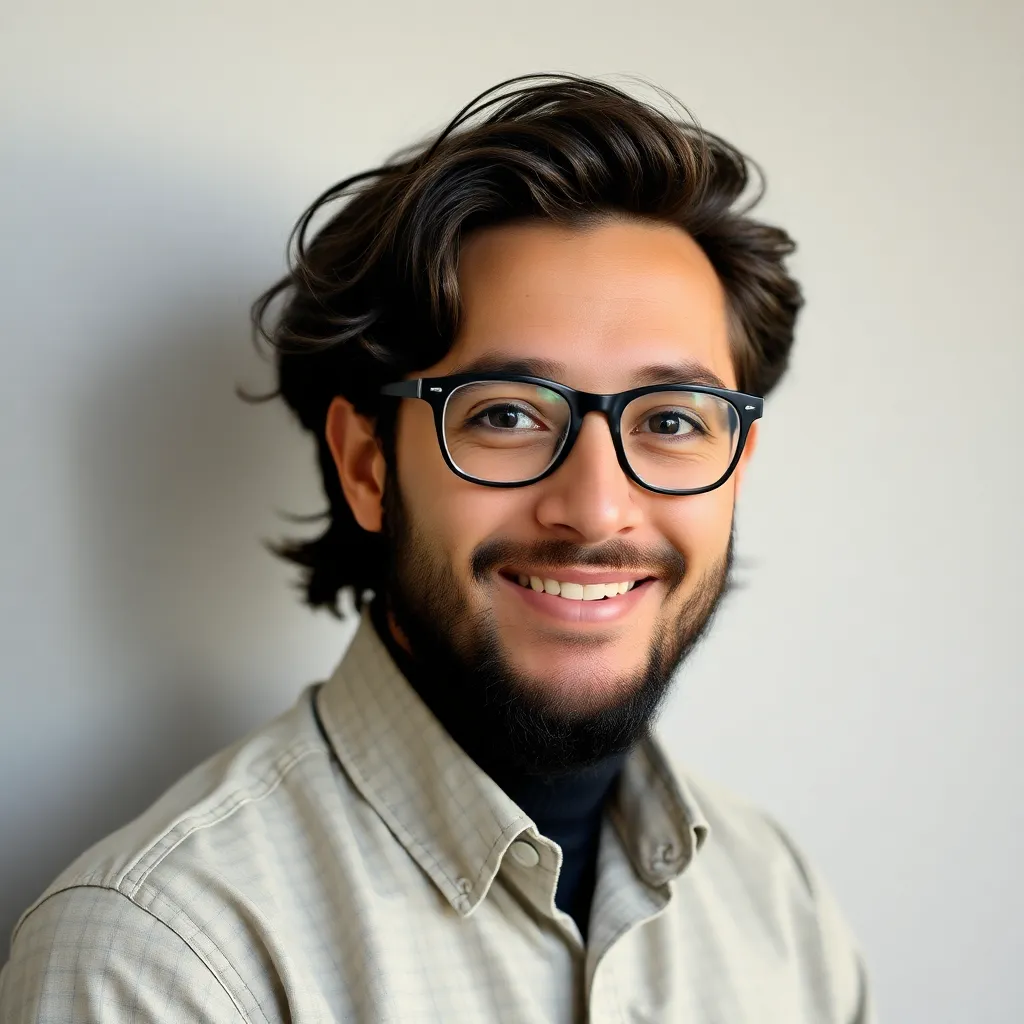
Kalali
Jun 11, 2025 · 4 min read
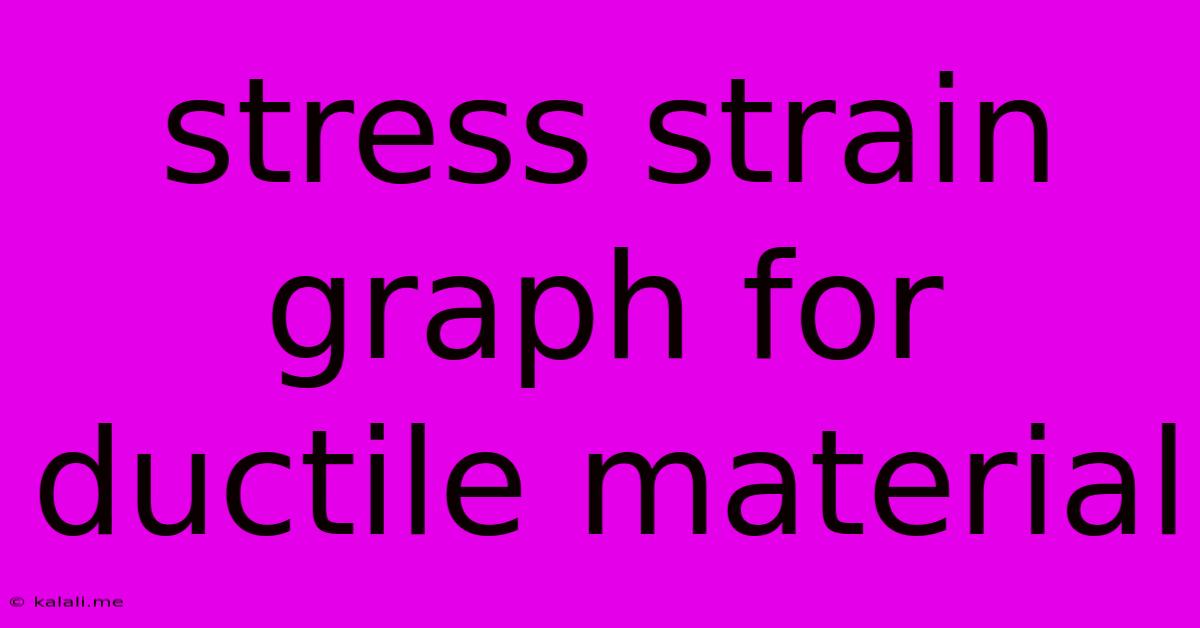
Table of Contents
Understanding the Stress-Strain Graph for Ductile Materials
The stress-strain graph, also known as the tensile test curve, is a fundamental tool in materials science for characterizing the mechanical properties of materials. This graph visually represents a material's response to an applied force, providing crucial insights into its strength, ductility, and toughness. This article delves into the specifics of the stress-strain graph for ductile materials, highlighting key regions and their significance. Understanding this graph is critical for engineers selecting materials for various applications.
What is a Ductile Material?
Before exploring the graph, it's important to define ductility. A ductile material is one that can undergo significant plastic deformation before fracture. This means it can be stretched, bent, or otherwise deformed considerably without breaking. Examples of ductile materials include mild steel, aluminum, and copper. This contrasts with brittle materials, which fracture with little to no plastic deformation.
The Key Regions of the Stress-Strain Graph for Ductile Materials
The typical stress-strain curve for a ductile material exhibits several distinct regions:
-
Elastic Region: This initial, linear portion of the curve represents elastic deformation. In this region, the material deforms proportionally to the applied stress, and upon removal of the load, it returns to its original shape. The slope of this region is known as Young's modulus (E), a measure of the material's stiffness or resistance to elastic deformation. Hooke's Law, which states stress is proportional to strain, governs this region. The proportional limit marks the end of perfectly linear elastic behavior.
-
Yield Point: This point marks the transition from elastic to plastic deformation. Beyond this point, the material undergoes permanent deformation, even after the load is removed. The yield point is often defined by the yield strength (σy), the stress at which a specified amount of permanent deformation (e.g., 0.2%) occurs. This is crucial for engineering design as it represents the stress level beyond which permanent deformation begins. Some materials exhibit a clear yield point, while others show a gradual transition.
-
Plastic Region: This region extends from the yield point to the ultimate tensile strength. Here, significant plastic deformation occurs. The material stretches considerably, exhibiting substantial changes in its dimensions. Strain hardening, also known as work hardening, is observed in this region; the material becomes stronger and harder with increasing deformation. This is due to the dislocation movements and interactions within the material's crystal structure.
-
Ultimate Tensile Strength (UTS): This is the maximum stress the material can withstand before necking begins. Necking is a localized reduction in the cross-sectional area of the material. It signifies the onset of material failure. The UTS is a critical parameter for determining the material's maximum load-carrying capacity.
-
Fracture Point: This is the point at which the material finally breaks. The stress at fracture is generally lower than the UTS because of the reduced cross-sectional area due to necking. The strain at fracture indicates the material's ductility. A higher strain at fracture signifies greater ductility.
Factors Affecting the Stress-Strain Curve
Several factors influence the shape and characteristics of the stress-strain curve for ductile materials, including:
- Temperature: Higher temperatures generally reduce the yield strength and UTS and increase ductility.
- Strain rate: Higher strain rates tend to increase the yield strength and UTS but decrease ductility.
- Material composition: Alloying elements and impurities significantly affect the mechanical properties and consequently, the stress-strain curve.
- Pre-existing defects: Microstructural features like voids or inclusions can influence the material's behavior, particularly at higher strains.
Applications and Significance
Understanding the stress-strain curve is paramount in various engineering applications. It enables engineers to:
- Select appropriate materials for specific applications based on required strength, ductility, and toughness.
- Design structures and components that can withstand anticipated loads without failure.
- Predict material behavior under various loading conditions.
- Optimize material processing techniques to improve mechanical properties.
In conclusion, the stress-strain graph is an invaluable tool for characterizing the mechanical behavior of ductile materials. Understanding its various regions and the factors influencing its shape is crucial for engineers and materials scientists alike in designing reliable and efficient structures and components. The data obtained from this simple yet informative test provides the foundation for material selection and structural design across numerous industries.
Latest Posts
Latest Posts
-
How Many Pounds Are In 900 Grams
Jul 01, 2025
-
How Long Does It Take To Drive 20 Miles
Jul 01, 2025
-
How Many Cups Is One Pound Of Pasta
Jul 01, 2025
-
How Many People Does A Gallon Of Tea Serve
Jul 01, 2025
-
How Many 750 Ml In A Gallon
Jul 01, 2025
Related Post
Thank you for visiting our website which covers about Stress Strain Graph For Ductile Material . We hope the information provided has been useful to you. Feel free to contact us if you have any questions or need further assistance. See you next time and don't miss to bookmark.