What Kind Of Energy Transformation Happens In An Eletric Motor
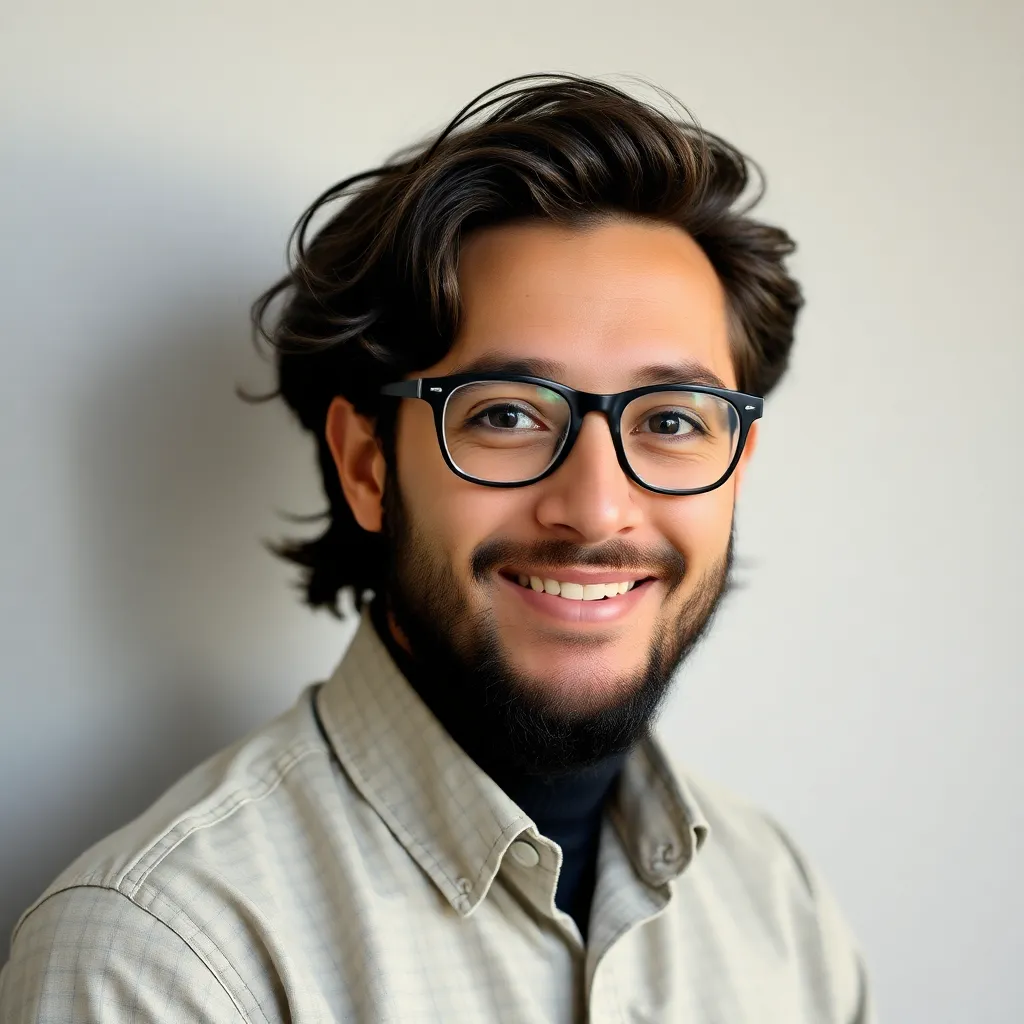
Kalali
Apr 08, 2025 · 6 min read
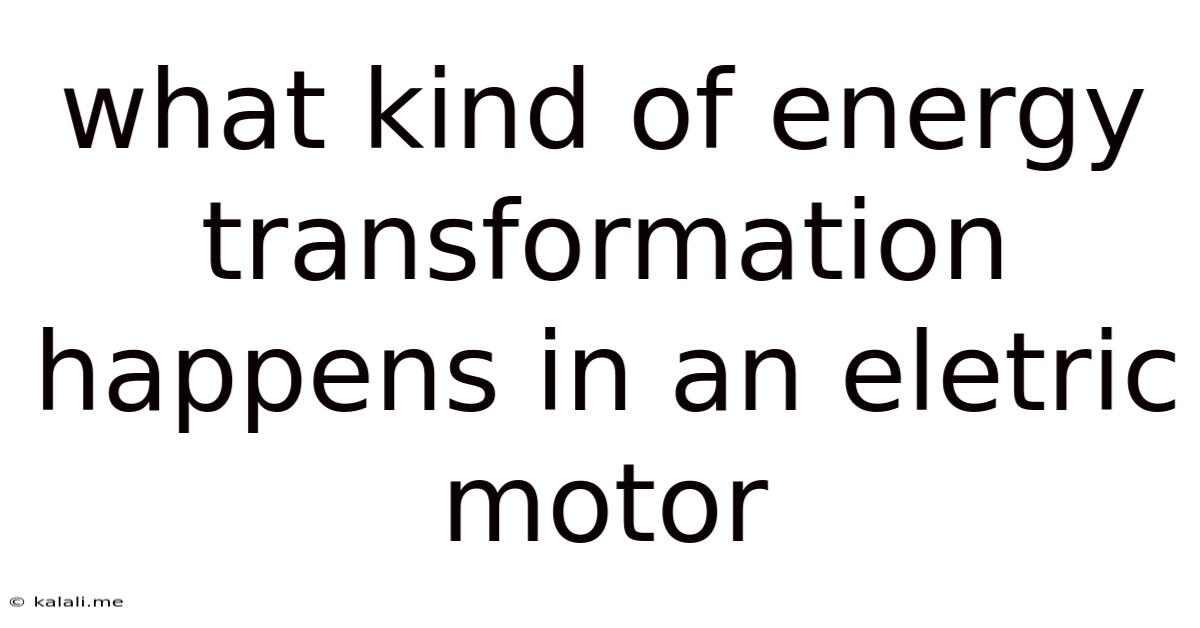
Table of Contents
The Amazing Energy Transformation Within an Electric Motor: From Electricity to Motion
Electric motors are ubiquitous in modern life, powering everything from our smartphones to industrial machinery. Understanding the energy transformations within these devices is crucial for appreciating their functionality and efficiency. This article delves into the fascinating physics behind electric motor operation, exploring the intricate dance between electrical energy and mechanical work. We'll cover different types of motors, their operating principles, and the losses that inevitably accompany this energy conversion. By the end, you'll have a comprehensive understanding of the energy transformation at the heart of these remarkable machines.
Meta Description: Discover the intricate energy transformation within electric motors, from electrical energy to mechanical motion. This comprehensive guide explores various motor types, their operating principles, efficiency, and common losses.
The Fundamental Principle: Electromagnetic Induction
At the heart of every electric motor lies the principle of electromagnetic induction, a cornerstone of physics discovered by Michael Faraday. This principle states that a changing magnetic field induces an electromotive force (EMF) – a voltage – in a nearby conductor. In electric motors, this principle is harnessed in reverse: an electric current creates a magnetic field, which then interacts with another magnetic field to produce rotational motion.
This interaction is governed by the fundamental force of magnetism. When a current flows through a conductor placed within a magnetic field, it experiences a force. The direction of this force is determined by Fleming's left-hand rule, a handy mnemonic device used to predict the direction of motion. This force, acting on multiple conductors arranged strategically, is what generates the torque – the rotational force – that drives the motor's shaft.
Types of Electric Motors and Their Energy Transformations
Electric motors come in various types, each employing slightly different mechanisms to achieve the same fundamental energy transformation. The most common types include:
-
DC Motors: Direct current (DC) motors use a direct current source to generate a magnetic field. These motors typically employ a commutator, a rotating switch that reverses the current direction in the motor windings, ensuring continuous rotation. The energy transformation in a DC motor involves converting the electrical energy from the DC source into rotational kinetic energy through the interaction of the magnetic fields generated by the stator (stationary part) and rotor (rotating part). The commutator plays a crucial role in maintaining the correct direction of torque.
-
AC Motors: Alternating current (AC) motors utilize alternating current as their power source. The changing current in the stator windings produces a rotating magnetic field, which interacts with the rotor windings to induce current and generate torque. This rotating magnetic field eliminates the need for a commutator, simplifying the motor's construction and enhancing its durability. AC motors are further categorized into several types, including:
-
Induction Motors: These are the most prevalent type of AC motor, characterized by their simplicity and robustness. They operate on the principle of electromagnetic induction, where the rotating magnetic field in the stator induces currents in the rotor, creating a magnetic field that interacts with the stator field to produce torque. The energy transformation in an induction motor involves the conversion of electrical energy from the AC source into rotational kinetic energy via electromagnetic induction. Slip, the difference between the synchronous speed of the rotating magnetic field and the actual rotor speed, is a key characteristic of induction motors.
-
Synchronous Motors: In contrast to induction motors, synchronous motors run at a constant speed, synchronized with the frequency of the AC power supply. These motors typically require a separate excitation source to generate the rotor's magnetic field, leading to precise speed control. The energy transformation is similar to induction motors, but the synchronous operation results in higher efficiency and better power factor.
-
Stepper Motors: Stepper motors provide precise rotational control, moving in discrete steps rather than continuous rotation. They are commonly used in applications requiring accurate positioning, such as 3D printers and CNC machines. The energy transformation here still involves converting electrical energy to rotational motion, but the control mechanism is distinctly different, involving sequential energization of the motor's windings.
-
Losses in the Energy Transformation Process
While electric motors are remarkably efficient in converting electrical energy into mechanical work, some energy is inevitably lost during the process. These losses can be categorized as follows:
-
Copper Losses (I²R Losses): These losses occur due to the resistance of the motor windings. The heat generated by the current flowing through these windings reduces the overall efficiency. Minimizing the resistance of the windings through the use of high-conductivity materials is crucial to reduce these losses.
-
Iron Losses (Core Losses): These losses occur in the motor's core due to hysteresis and eddy currents. Hysteresis losses result from the energy required to repeatedly magnetize and demagnetize the core material. Eddy currents are circulating currents induced in the core by the changing magnetic field, generating heat and wasting energy. Using specialized core materials with low hysteresis and high resistivity helps to minimize these losses.
-
Mechanical Losses: These losses include friction in the bearings and windage losses due to air resistance. Proper lubrication and optimized design can mitigate these losses.
-
Stray Load Losses: These losses encompass a variety of smaller effects, including leakage flux, stray currents, and losses in the motor's end windings. Accurate modeling and careful design are essential for minimizing these losses.
Efficiency and Power Factor
The efficiency of an electric motor is a crucial metric that represents the ratio of mechanical output power to electrical input power. A higher efficiency indicates less energy waste. Several factors influence motor efficiency, including design, operating conditions, and maintenance. Optimizing the motor design to minimize losses is paramount in achieving high efficiency.
The power factor, another important characteristic, represents the ratio of real power to apparent power. A low power factor indicates that a significant portion of the apparent power is not contributing to the useful work done by the motor, leading to increased energy consumption. Improving the power factor through the use of power factor correction capacitors is often implemented to enhance the overall system efficiency.
Advanced Motor Technologies and Future Trends
Research and development in electric motor technology continue to push the boundaries of efficiency and performance. Some notable advancements include:
-
Permanent Magnet Motors: These motors use permanent magnets instead of electromagnets for one of the magnetic fields, leading to higher efficiency and power density.
-
Switched Reluctance Motors: These motors offer robust construction and high efficiency, making them suitable for demanding applications.
-
Brushless DC Motors: These motors eliminate the need for brushes and commutators, resulting in longer lifespan and higher efficiency.
-
High-Temperature Superconducting Motors: The use of superconducting materials promises significantly increased efficiency by eliminating resistive losses in the windings.
The future of electric motor technology likely involves further miniaturization, enhanced efficiency, improved power density, and the integration of advanced control systems for precise and responsive operation. The development of new materials and manufacturing techniques will play a crucial role in achieving these goals.
Conclusion: A Symphony of Energy Transformation
The energy transformation within an electric motor is a fascinating interplay of electrical and magnetic phenomena. From the fundamental principles of electromagnetic induction to the sophisticated designs of modern motors, the journey from electrical energy to mechanical work is a testament to human ingenuity. Understanding the intricacies of this transformation, including the various types of motors, their operating principles, and the inherent losses, is crucial for designing, operating, and optimizing these indispensable machines for a wide array of applications. Continuous innovation promises even greater efficiency and performance in the years to come, solidifying the electric motor's role as a cornerstone of modern technology.
Latest Posts
Latest Posts
-
How Many Mm Are In One M
Apr 17, 2025
-
Common Multiples Of 8 And 15
Apr 17, 2025
-
How Long Is 23 Cm In Inches
Apr 17, 2025
-
What Are The Monomers Of Dna
Apr 17, 2025
-
How Many Kilos Is 17 Pounds
Apr 17, 2025
Related Post
Thank you for visiting our website which covers about What Kind Of Energy Transformation Happens In An Eletric Motor . We hope the information provided has been useful to you. Feel free to contact us if you have any questions or need further assistance. See you next time and don't miss to bookmark.