A Hydraulic Motor Converts Fluid Pressure To
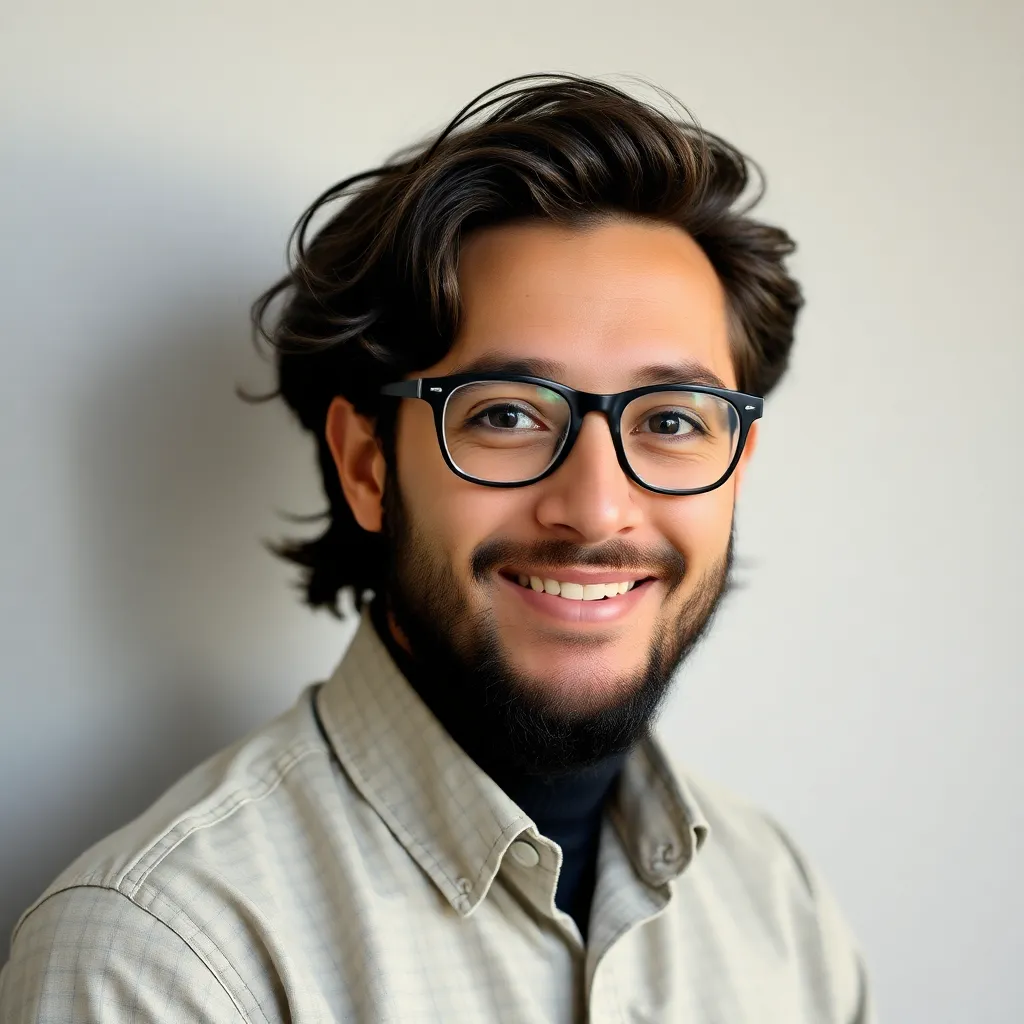
Kalali
Apr 14, 2025 · 7 min read
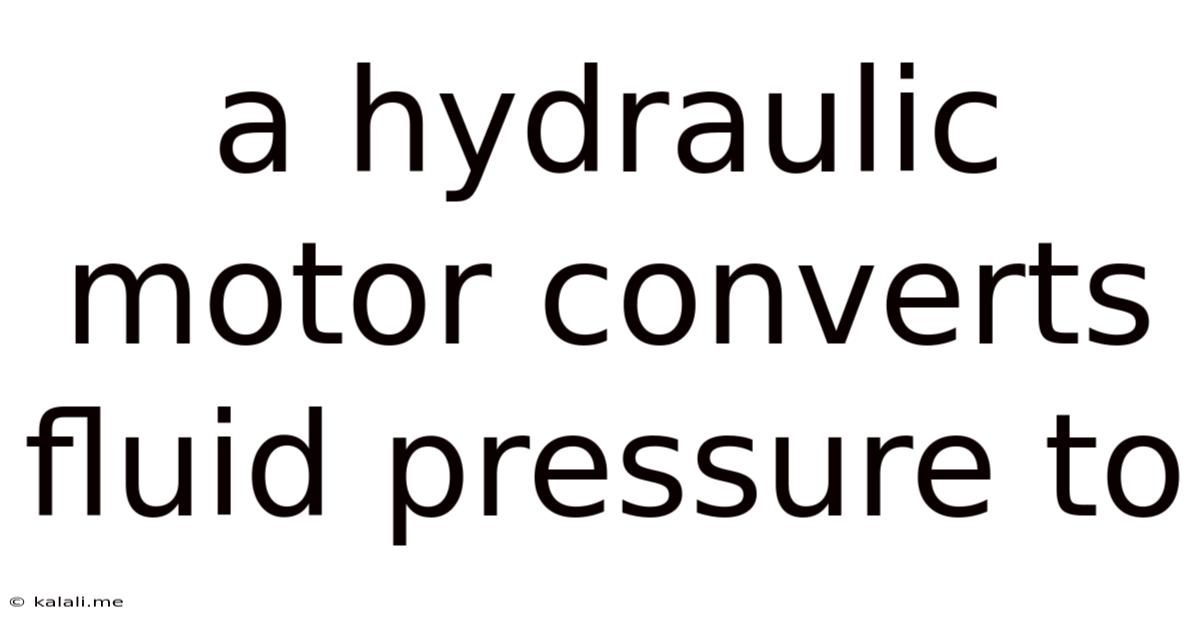
Table of Contents
A Hydraulic Motor: Converting Fluid Pressure to Rotational Motion
Hydraulic motors are powerful and versatile devices that convert the energy of pressurized fluid into rotational mechanical energy. This conversion process is crucial in various industries, from heavy machinery and construction to aerospace and robotics. Understanding how these motors work, their types, applications, and advantages is vital for anyone working with hydraulic systems or interested in fluid power technology. This article will delve deep into the fascinating world of hydraulic motors, explaining their functionality, key components, and diverse applications.
Meta Description: Discover the inner workings of hydraulic motors – how they transform fluid pressure into rotational motion, their various types, applications, and advantages in diverse industries. Learn about positive displacement motors and their crucial role in power transmission.
Understanding the Fundamentals of Hydraulic Motor Operation
At its core, a hydraulic motor operates on the principle of positive displacement. This means that a fixed volume of hydraulic fluid is drawn into the motor, and its pressure is used to generate a controlled rotational output. This differs from other types of motors, such as electric motors, where energy conversion is based on electromagnetic principles. The pressurized fluid, typically oil, is supplied under high pressure from a hydraulic pump. This pressure acts upon the internal components of the motor, forcing them to rotate, ultimately driving a connected mechanical load. The speed and torque of the motor are directly related to the pressure and flow rate of the hydraulic fluid. Higher pressure generally results in higher torque, while a higher flow rate leads to higher rotational speed.
Key Components of a Hydraulic Motor
While the specific components may vary depending on the type of hydraulic motor, several essential parts are common to most designs:
- Housing: This encloses the internal components, providing structural support and containing the hydraulic fluid.
- Rotor: The rotating element of the motor, converting fluid pressure into rotational motion.
- Displacer: (Present in certain designs) This component interacts with the hydraulic fluid to create the displacement.
- Valves: These control the flow of hydraulic fluid into and out of the motor, regulating speed and direction.
- Bearings: Support the rotor and reduce friction, ensuring smooth operation.
- Shaft: Transmits the rotational motion from the rotor to the external load.
- Ports: Inlet and outlet points for the hydraulic fluid.
Types of Hydraulic Motors
Hydraulic motors are broadly classified into two main categories: positive displacement motors and non-positive displacement motors. However, non-positive displacement motors are far less common and generally less efficient, so the vast majority of applications utilize positive displacement motors. Within positive displacement motors, there are several subtypes, each with its own unique characteristics and applications:
1. Gear Motors:
Gear motors use meshing gears to displace hydraulic fluid. The high-pressure fluid enters between the gear teeth, forcing the gears to rotate. These motors are relatively simple in design, compact, and offer high efficiency at lower speeds. However, their efficiency decreases at higher speeds. They are commonly found in applications requiring moderate torque and speed, such as agricultural machinery and material handling equipment.
2. Vane Motors:
Vane motors feature a rotor with a series of vanes that slide radially in slots. As high-pressure fluid enters the chamber between the vanes, it forces the rotor to rotate. Vane motors provide smooth and relatively quiet operation compared to gear motors. They are often preferred in applications where low noise and vibration are crucial, such as printing presses and machine tools.
3. Piston Motors:
Piston motors are considered the most powerful and efficient type of hydraulic motor. They utilize multiple pistons that reciprocate in a cylindrical housing. The pressurized fluid forces the pistons to move, creating rotational motion. Piston motors are further classified into several subtypes based on their design, including:
- Radial Piston Motors: The pistons are arranged radially around the central shaft. This design allows for high torque and power output, making them suitable for heavy-duty applications such as excavators and bulldozers.
- Axial Piston Motors: The pistons are arranged axially, parallel to the shaft. These are characterized by high power density and efficient operation over a wide speed range. They are frequently employed in applications demanding high power and precision, such as robotic manipulators and aircraft control systems.
- Bent-Axis Piston Motors: These combine features of both radial and axial designs, providing a combination of high power density and variable displacement capability.
4. Other Types:
While less prevalent, other types of hydraulic motors exist, including:
- Gerotor Motors: These motors utilize a gerotor mechanism which consists of an internal and external rotor with different numbers of lobes. The fluid is trapped between the lobes and transferred to produce rotation.
- Swashplate Motors: These motors use a swashplate mechanism to control the stroke of pistons and regulate the motor's speed and torque. Often found in applications requiring precise control and variable displacement.
Advantages of Hydraulic Motors
Hydraulic motors offer several key advantages over other types of motors:
- High Torque at Low Speeds: Hydraulic motors can generate exceptionally high torque at low speeds, making them ideal for applications requiring high starting torque.
- Precise Control: The flow rate and pressure of the hydraulic fluid can be precisely controlled, allowing for accurate speed and torque regulation.
- Reversibility: Most hydraulic motors are easily reversible, simply by changing the direction of fluid flow.
- Compact Design: Compared to equivalent electric motors generating the same power, hydraulic motors often have a smaller physical size.
- High Power-to-Weight Ratio: This makes them suitable for mobile and portable equipment.
- Overload Protection: Hydraulic systems often incorporate safety features that protect the motor from overload conditions.
Applications of Hydraulic Motors
The versatility and capabilities of hydraulic motors make them indispensable across a wide range of applications, including:
- Construction Equipment: Excavators, bulldozers, cranes, and loaders rely heavily on hydraulic motors for their powerful and precise movements.
- Agricultural Machinery: Tractors, harvesters, and other agricultural equipment use hydraulic motors for various functions, including steering, lifting, and powering implements.
- Material Handling Equipment: Forklifts, conveyor systems, and other material handling equipment use hydraulic motors for lifting, transporting, and positioning materials.
- Industrial Machinery: Hydraulic motors are used in a variety of industrial applications, including machine tools, presses, and packaging machines.
- Aerospace: Aircraft control systems and flight actuators often utilize high-performance hydraulic motors.
- Robotics: Precision and power make hydraulic motors suitable for robotic manipulators and other robotic applications.
- Marine Applications: Steering gear, winches, and other components in ships and other marine vessels often employ hydraulic motors.
- Automotive: While less common than electric motors, hydraulic motors can be found in some specialized automotive applications, such as power steering systems in older vehicles.
Selecting the Right Hydraulic Motor
Choosing the appropriate hydraulic motor for a specific application requires careful consideration of several factors:
- Required Torque and Speed: The application's demands for torque and speed will dictate the type and size of the motor needed.
- Operating Pressure: The hydraulic system's operating pressure must be compatible with the motor's specifications.
- Efficiency Requirements: The desired efficiency level will influence the choice of motor type and design.
- Environmental Conditions: Temperature, humidity, and other environmental factors should be considered.
- Space Constraints: The available space for the motor will impact the selection process.
- Cost: The initial cost, maintenance costs, and lifecycle costs of different motor types should be evaluated.
Maintenance and Troubleshooting
Regular maintenance is crucial for ensuring the longevity and efficient operation of hydraulic motors. This includes:
- Regular Fluid Changes: Replacing the hydraulic fluid at recommended intervals helps remove contaminants and maintain lubrication.
- Filter Inspection and Replacement: Clean or replace filters to prevent debris from damaging the motor.
- Leak Detection and Repair: Promptly address any leaks to prevent fluid loss and potential damage.
- Bearing Inspection and Lubrication: Regularly inspect and lubricate bearings as needed to minimize friction and wear.
Understanding the potential issues and troubleshooting techniques is equally important. Common problems include low output torque, excessive noise, and leaks. Addressing these issues promptly prevents further damage and ensures the continued operation of the system.
Conclusion
Hydraulic motors are remarkable machines that efficiently convert the energy of pressurized fluid into rotational mechanical energy. Their diverse types, robust performance, and adaptability to various applications underscore their vital role across numerous industries. By understanding their working principles, components, advantages, and applications, engineers, technicians, and anyone involved in fluid power systems can effectively leverage these powerful devices for efficient and reliable operation in a wide range of tasks. The continuous evolution of hydraulic motor technology promises further advancements, enhancing their capabilities and expanding their applications in the future.
Latest Posts
Latest Posts
-
What Is 1 3 Of A Pound
Apr 15, 2025
-
How Many Cups In 14 5 Oz
Apr 15, 2025
-
What Percent Is 3 Of 8
Apr 15, 2025
-
Cuanto Es 11 Centimetros En Pulgadas
Apr 15, 2025
-
What Is 2 To The Power Of 8
Apr 15, 2025
Related Post
Thank you for visiting our website which covers about A Hydraulic Motor Converts Fluid Pressure To . We hope the information provided has been useful to you. Feel free to contact us if you have any questions or need further assistance. See you next time and don't miss to bookmark.