Do You Need Insulation Wrapped Around Your Fractional Distillation Apparatus
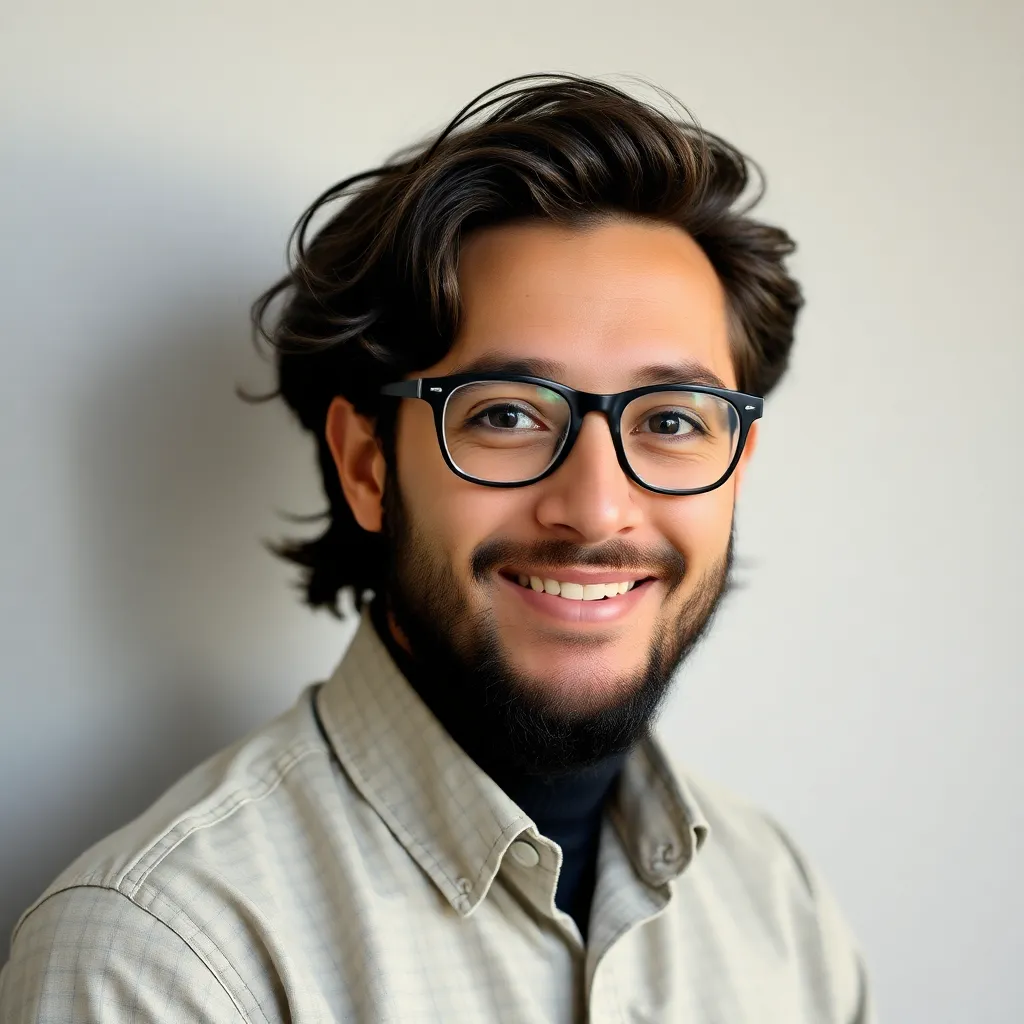
Kalali
Apr 06, 2025 · 6 min read

Table of Contents
Do You Need Insulation Wrapped Around Your Fractional Distillation Apparatus?
Fractional distillation, a crucial technique in chemistry and chemical engineering, separates liquid mixtures into their individual components based on their boiling points. While the core principle is relatively straightforward, optimizing the process for efficiency and accuracy involves a multitude of factors. One such factor, often debated, is the necessity of insulation around the fractional distillation apparatus. This article delves deep into this question, exploring the advantages, disadvantages, and ultimately, helping you determine if insulation is right for your fractional distillation setup.
The Science Behind Fractional Distillation
Before we dive into insulation, let's briefly revisit the fundamentals of fractional distillation. The process relies on the repeated vaporization and condensation of a liquid mixture as it travels up a fractionating column. The column is designed with a large surface area to promote efficient heat transfer and equilibrium between the liquid and vapor phases. Components with lower boiling points vaporize more readily and rise higher in the column, while those with higher boiling points remain primarily in the liquid phase at lower levels.
The efficiency of the separation depends on several factors, including the length and design of the column, the temperature gradient, and the rate of heating. A well-designed column with numerous theoretical plates (representing the number of vapor-liquid equilibrium stages) enhances the separation process. This is where insulation plays a critical role.
The Role of Insulation in Fractional Distillation
Insulation, typically a material with low thermal conductivity (like glass wool, fiberglass, or even aluminum foil), is wrapped around the fractionating column to minimize heat loss to the surrounding environment. By reducing heat loss, insulation significantly impacts the process in several key ways:
1. Improved Temperature Gradient:
A consistent temperature gradient along the column is crucial for effective separation. Without insulation, heat is lost to the surroundings, creating temperature variations that can lead to inefficient separation and reduced purity of the collected fractions. Insulation helps maintain a smoother, more gradual temperature gradient, thereby improving the efficiency of the separation process. This is particularly important for complex mixtures with closely boiling components.
2. Enhanced Vapor-Liquid Equilibrium:
The efficiency of fractional distillation hinges on establishing equilibrium between the vapor and liquid phases at each point in the column. Heat loss disrupts this equilibrium, reducing the number of effective theoretical plates and consequently, the quality of the separation. Insulation helps maintain a closer approach to equilibrium, leading to sharper separations and higher purity products.
3. Reduced Energy Consumption:
Insulation minimizes heat loss, meaning that less energy is required to maintain the desired temperature gradient and complete the distillation process. This translates into both cost savings and environmental benefits, as less energy consumption reduces carbon footprint. This is particularly beneficial for large-scale fractional distillation operations.
When Insulation is Crucial: Considerations for Specific Scenarios
While insulation generally improves the fractional distillation process, its necessity is influenced by several contextual factors:
1. The Complexity of the Mixture:
For simple binary mixtures with significantly different boiling points, the need for insulation may be less critical. The separation might still be quite effective even without insulation, although the yield and purity will be slightly reduced. However, for more complex mixtures with closely boiling components, insulation becomes considerably more important. The enhanced temperature gradient and equilibrium provided by insulation significantly increase the chances of achieving a successful separation of these components.
2. The Scale of the Distillation:
In small-scale laboratory distillations, the impact of heat loss might be relatively minor. The surface area to volume ratio is higher, and heat loss becomes less of a significant factor. Large-scale industrial distillations, on the other hand, experience far greater heat loss. Insulation is essentially mandatory in these cases to maintain efficient operation and minimize energy consumption.
3. The Boiling Points of Components:
Distilling mixtures with high boiling points increases the overall heat requirement, rendering heat loss a more significant concern. If you're working with components that require higher temperatures for distillation, insulation's ability to retain heat and minimize energy waste becomes even more pronounced. Conversely, for components with very low boiling points, heat loss may have a less substantial impact due to the lower heat requirements of the process.
4. The Ambient Temperature:
The ambient temperature significantly impacts the effectiveness of insulation. In colder environments, heat loss is accelerated, making insulation even more essential to maintain optimal operating conditions. In warmer environments, while insulation remains beneficial, its impact might be less dramatic due to the reduced rate of heat loss.
Types of Insulation and Their Suitability
Several materials can be used for insulation in fractional distillation, each with its own advantages and disadvantages:
-
Glass Wool: A commonly used and relatively inexpensive insulator, it is efficient at trapping air and reducing heat transfer. However, it's somewhat fragile and can release small fibers.
-
Fiberglass: Similar to glass wool in its insulating properties, fiberglass is more durable and less prone to fiber release. It comes in various forms, including blankets and sleeves, making it a versatile option.
-
Aluminum Foil: While not a primary insulator, aluminum foil is often used as a reflective layer to minimize radiant heat loss. It's often used in conjunction with other insulation materials.
-
Silicone Rubber Sleeves/Tubing: A very suitable choice for insulation in particular because it allows visual observation of the experiment. It is also reusable and easy to apply. However, this material might not be the best for high temperatures and for distilling components that may be aggressive to silicone.
The choice of insulation material will depend on factors like the temperature range, the chemical compatibility of the materials with the compounds being distilled, and cost considerations.
The Downsides of Insulation
While generally beneficial, insulation isn't without its potential drawbacks:
-
Increased Condensation: Insulation can sometimes lead to increased condensation within the column, potentially interfering with the separation process. This can occur if the insulation is too thick, hindering adequate heat dissipation and causing the column to become excessively saturated with condensed vapor. The proper thickness of insulation is therefore very important in practice.
-
Difficulty in Monitoring Temperature: Insulation can make it harder to accurately monitor the temperature at various points along the column. This is partially mitigated by using thermocouples and other temperature sensors strategically placed within the apparatus.
-
Cost: Insulation material adds to the overall cost of the setup. It's a trade-off between the improved efficiency and the additional expense.
Conclusion: A Case-by-Case Assessment
The question of whether you need insulation wrapped around your fractional distillation apparatus doesn't have a simple yes or no answer. The decision hinges on a careful consideration of factors such as the complexity of the mixture, the scale of the distillation, the boiling points of the components, the ambient temperature, and the cost-benefit analysis.
For complex mixtures with closely boiling points, large-scale distillations, and high boiling point components, insulation is highly recommended, even essential, for achieving efficient and accurate separation. The energy savings and improved purity often outweigh the added cost and potential minor drawbacks. For simpler distillations on a smaller scale, the benefits of insulation might be less pronounced, and the decision might depend on other factors and individual priorities. In such cases, a trial run without insulation followed by a comparison with a run using insulation might be helpful to determine the optimal approach. Remember to always prioritize safety and choose appropriate insulation materials considering chemical compatibility and the operating temperature range.
Latest Posts
Latest Posts
-
Half Of A Pint Equals How Many Cups
Apr 08, 2025
-
6 Cm Is How Many Mm
Apr 08, 2025
-
What Is 50 F In C
Apr 08, 2025
-
Cuanto Es 5 5 Pies En Centimetros
Apr 08, 2025
-
11 Is What Percent Of 20
Apr 08, 2025
Related Post
Thank you for visiting our website which covers about Do You Need Insulation Wrapped Around Your Fractional Distillation Apparatus . We hope the information provided has been useful to you. Feel free to contact us if you have any questions or need further assistance. See you next time and don't miss to bookmark.