Stress Strain Diagram For Brittle Material
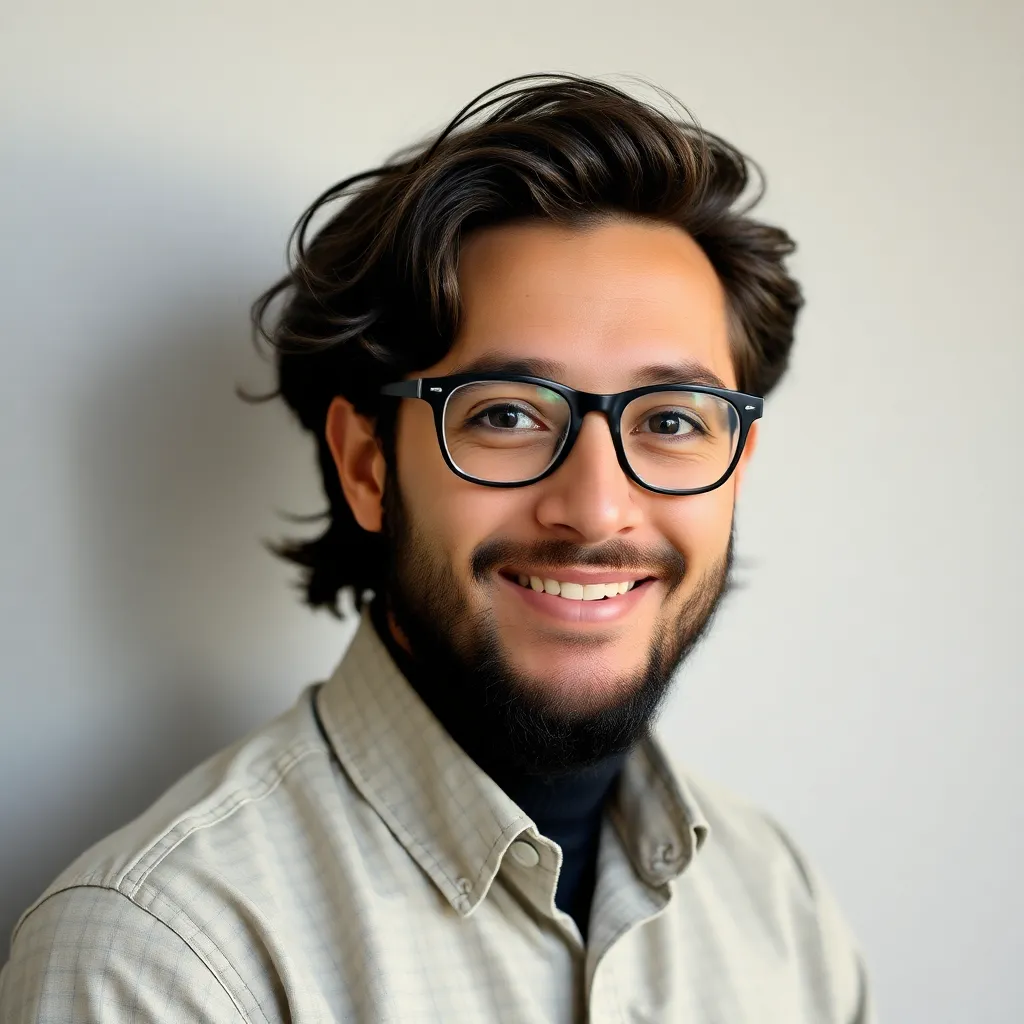
Kalali
Jun 11, 2025 · 3 min read
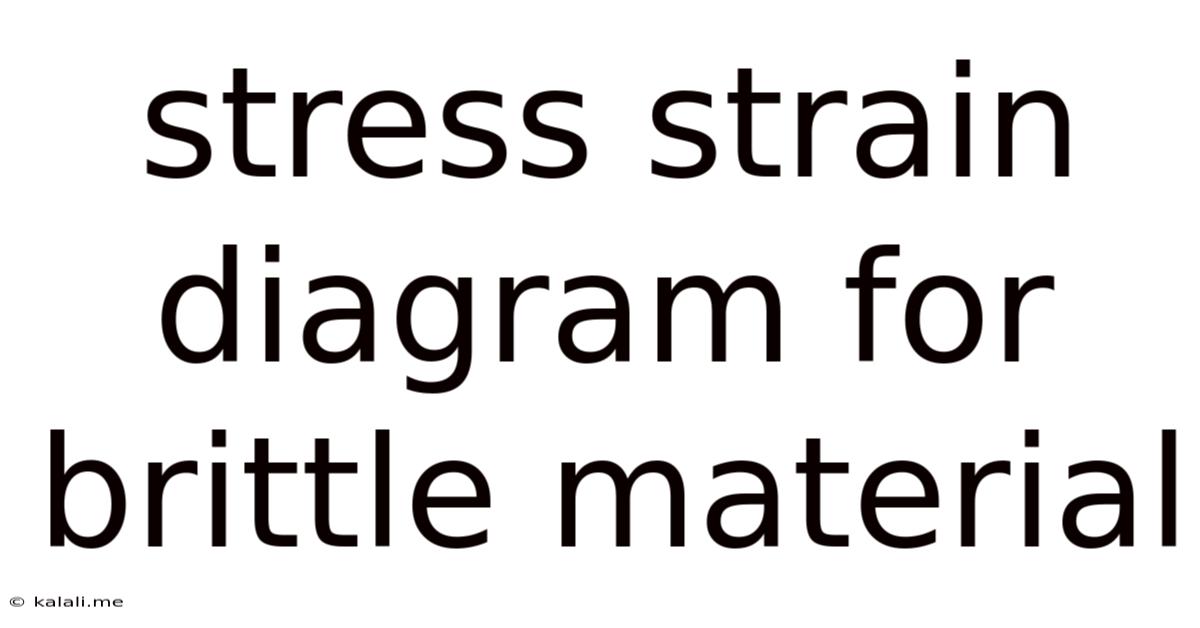
Table of Contents
Stress-Strain Diagram for Brittle Materials: A Comprehensive Guide
Understanding the mechanical behavior of materials is crucial in engineering design. This article delves into the stress-strain diagram for brittle materials, explaining its unique characteristics and implications for material selection and application. We'll explore the key differences compared to ductile materials, focusing on the absence of yielding and the sudden fracture.
Brittle materials, unlike their ductile counterparts, exhibit minimal plastic deformation before failure. This means they break or fracture suddenly with little to no warning. This characteristic is clearly reflected in their stress-strain diagrams.
Key Features of a Brittle Material Stress-Strain Diagram
The stress-strain diagram for a brittle material is notably different from that of a ductile material. Here's a breakdown of its key features:
-
Linear Elastic Region: Similar to ductile materials, brittle materials initially exhibit a linear elastic region. This means stress and strain are directly proportional, following Hooke's Law. The slope of this linear portion represents the Young's Modulus (E), indicating the material's stiffness or resistance to deformation.
-
Absence of Yield Point: This is a crucial difference. Brittle materials lack a clearly defined yield point – the point where plastic deformation begins. They transition directly from elastic deformation to fracture.
-
Fracture Point: The stress-strain curve ends abruptly at the fracture point. This is where the material fails catastrophically. The stress at fracture is known as the ultimate tensile strength (UTS), representing the maximum stress the material can withstand before breaking.
-
Little to No Necking: Unlike ductile materials which often exhibit necking (reduction in cross-sectional area) before fracture, brittle materials generally show minimal or no such behavior. The fracture often occurs relatively quickly.
-
High Modulus of Elasticity: Brittle materials often possess a high Young's Modulus, indicating their stiffness and resistance to elastic deformation. This high stiffness, however, doesn't translate to toughness, as they lack ductility.
-
Low Strain to Failure: The strain at the fracture point is significantly lower for brittle materials compared to ductile materials. This signifies their limited ability to deform before failure.
Comparing Brittle and Ductile Stress-Strain Diagrams
The contrasting behaviors are best understood by comparing the diagrams:
Feature | Brittle Material | Ductile Material |
---|---|---|
Elastic Region | Present, typically linear | Present, typically linear |
Yield Point | Absent | Clearly defined |
Plastic Region | Absent | Significant, showing considerable deformation |
Fracture | Sudden, without significant deformation | Often preceded by necking and significant deformation |
Strain to Failure | Low | High |
Examples of Brittle Materials
Common examples of brittle materials include:
- Ceramics: These materials, such as porcelain and glass, are known for their hardness and brittleness.
- Concrete: A widely used construction material, concrete exhibits brittle behavior under tensile stress.
- Cast Iron: A type of iron with a high carbon content, cast iron is relatively brittle compared to steel.
- Many Composites: Depending on the reinforcement and matrix materials, some composites may exhibit brittle fracture behavior.
- Glass: A classic example of a brittle material, known for its fragility and tendency to shatter under impact.
Implications for Engineering Design
The brittle nature of these materials necessitates careful consideration in engineering design. Since they fail suddenly, there's a lower tolerance for flaws or unexpected stress concentrations. Design strategies often focus on:
- Stress Concentration Reduction: Careful design to minimize sharp corners and stress risers.
- Safety Factors: Using significantly higher safety factors compared to designs using ductile materials.
- Fatigue Analysis: Addressing the potential for fatigue failure, even under relatively low cyclic loading.
- Material Selection: Choosing appropriate materials that possess sufficient strength and fracture toughness for the intended application.
Understanding the stress-strain diagram for brittle materials is fundamental for engineers and material scientists. By appreciating their unique mechanical properties and limitations, we can design safer and more reliable structures and components.
Latest Posts
Latest Posts
-
I Reject Your Reality And I Substitute My Own
Jul 01, 2025
-
5 X 5 X 5 X 5
Jul 01, 2025
-
How Many Cups In A 5th Of Vodka
Jul 01, 2025
-
How Much Is 20 Lbs Of Pennies Worth
Jul 01, 2025
-
How Much Is 20 Lb Of Pennies Worth
Jul 01, 2025
Related Post
Thank you for visiting our website which covers about Stress Strain Diagram For Brittle Material . We hope the information provided has been useful to you. Feel free to contact us if you have any questions or need further assistance. See you next time and don't miss to bookmark.